Do you love star quilts as much as I do? I’ll bet half the quilts I’ve made over the years contain star blocks. Susan of stitchedbysusan.com, a quilter whose work I very much admire, asked me the other day on Instagram about my “best tips for perfect star points.” I thought to myself, “That’s a good topic for a blog post!”
I’m always surprised — and yes, a little disappointed — when I see star quilts with the points cut off. With a little care that can be avoided completely.
To illustrate this post I’m using a 6″ Sawtooth Star block from my current project. It’s made up of four Flying Geese units which form the star points, a square in the middle of the block, and four smaller squares in the corners:
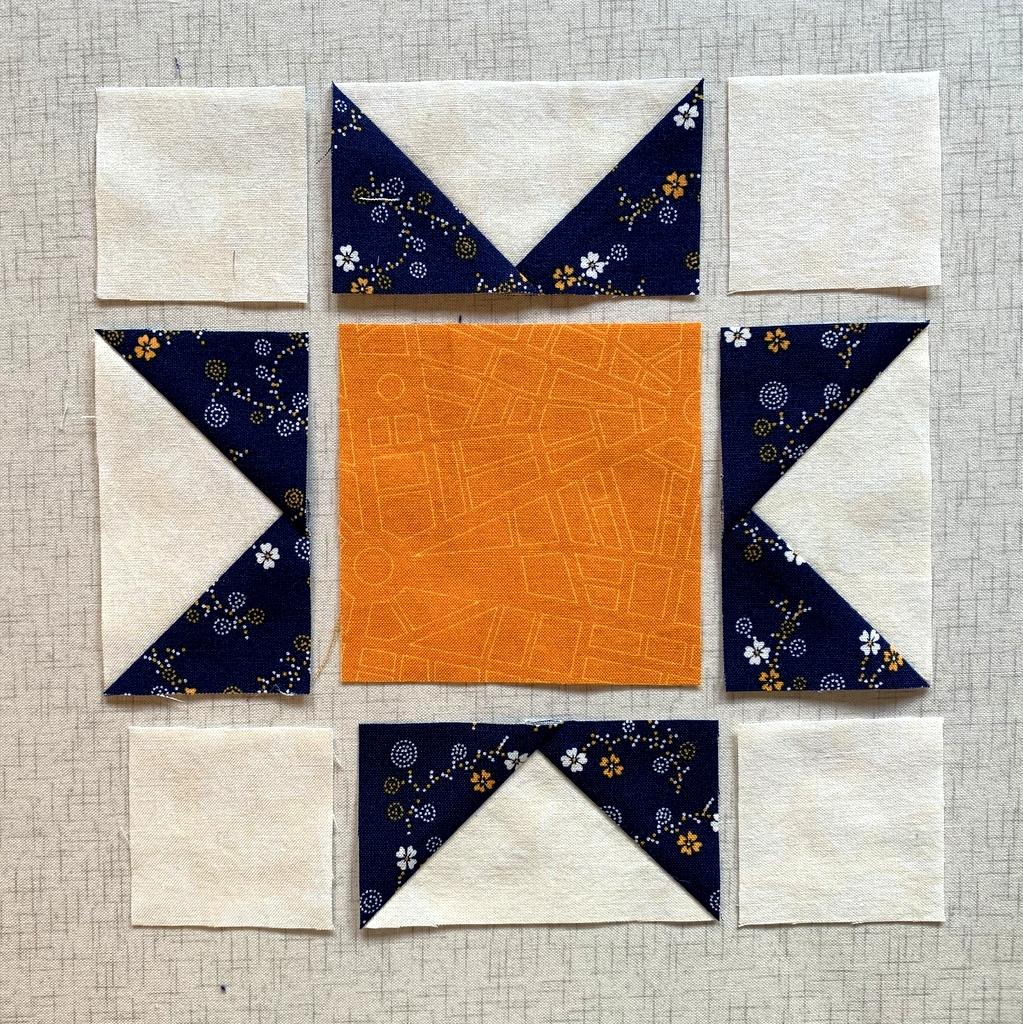
If you look at the four Flying Geese units you’ll notice that the points of the star go right to the corners, the outer edges of the units. If the seamline is off on either side of the corner by even an eighth of an inch, the star point is going to be off when it’s joined to the other pieces in the block. In a block this small, a sixteenth of an inch can make a difference.
Tip #1: Make sure the seamline intersects the corner precisely.
The easiest way to achieve this is to make the block slightly oversize and then trim to exact size with a ruler. This is especially true with star points because they contain diagonal seams and it’s all too easy to get some distortion when sewing and pressing them, especially if you use steam and press with a heavy hand like I do.
There are several excellent Flying Geese trimming rulers on the market (I have two that I love) but the truth is you can trim perfect star points with any ruler that has the proper angled degree line going to a corner. Because a traditional Flying Geese unit is always twice as long as it is high, that angle is 45 degrees. Virtually every quilting ruler has a 45 degree angle marked on it.
Tip #2: Don’t forget the No Surprises pin.
I have my teacher and mentor Billie Mahorney to thank for this tip. It’s one of the most valuable things I ever learned from her. The No Surprises pin is the one that goes at the end of every stitching line to make sure the two layers are still lined up when you get to the end. The feed dogs on a sewing machine don’t always feed the layers evenly, resulting in one layer coming up short. This is especially true with longer seams. No matter how short the stitching line, I never fail to put in the No Surprises pin.
In my block the first three seams are pinned and ready to chain sew. Because these pieces are so small I didn’t feel the need to do pinning other than the No Surprises pin:
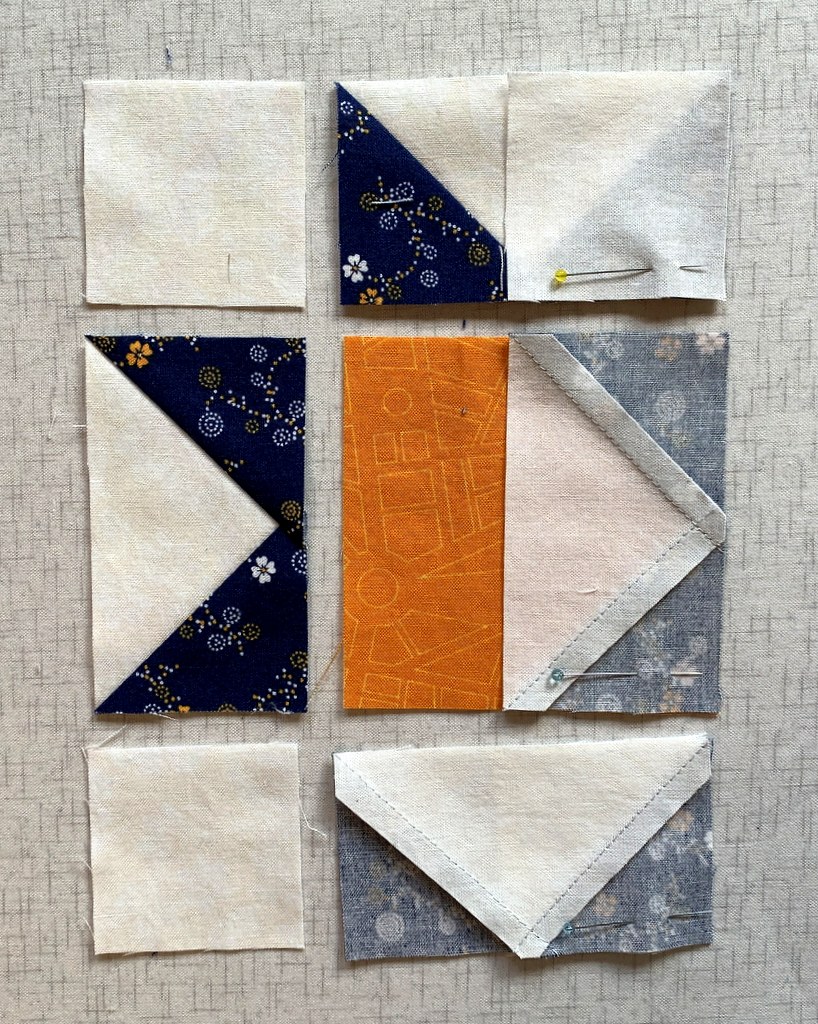
I have arranged the top and bottom pairs to be stitched so that I am stitching in the direction the diagonal seam was pressed (i.e. with the seam rather than against it).
On the middle pair I’m stitching on the side where I can see the intersection and make sure I cross it in the proper place (see Tip #3 below).
Here are the pieces chain stitched:

Look very carefully at this next photo for a preview of Tip #3:

Do you see how my stitching line joining the two pieces doesn’t cross at the exact top of the inverted V? It’s actually a couple of threads away from the point formed by the V and toward the raw edges.
When the stitching line is right on top of the point or — heaven forbid — a few threads on the inside, the point in the background fabric gets chopped off. This is where an accurate quarter-inch seam is so critical.
Tip #3: When approaching a point (in this case it’s the bottom of the V of a Flying Geese unit), don’t stitch exactly across the point where the stitching lines intersect; rather, sew a couple of threads away from the point and toward the raw edges. This little tip is what gives you a nice crisp point when the seam is pressed.
Tip #4: In order to achieve Tip #3, make sure you are using a foot that allows you to see the needle going in and out of the fabric. Most quarter-inch feet are “open toe,” allowing you to see the path the needle takes.
Take a look at the next photo. You can see that my star points in the top two pieces where the corner squares have been added are a quarter of an inch away from the edge — thus they won’t get chopped off when I sew them to another piece of fabric. In the bottom piece, which is the center of the block, the inside V of the background fabric is nice and sharp.

Tip #5: Sew seams with a regular quarter inch seam. This is not the time to go for a “scant quarter inch” because the point of your star will land inside the seam allowance when other pieces are sewn to the block. That’s another way star points get chopped off.
Now look at the picture again and notice how the seams are pressed. In the top two pieces the seams are pressed toward the outside (toward the corner squares). In the bottom piece, the seam is pressed toward the center square and away from the Flying Geese unit. My seams will nest when I’m ready to sew the units together.
Tip #6: Whenever possible, press away from the points, whether it’s the star points or the bottom of the V of a Flying Geese unit.
Tip #7: Whenever possible, press from the right side of the block. This helps prevent tiny pleats from being pressed in at the seamline, which often happens when blocks are pressed from the wrong side.
I’ve added the other pieces of my Sawtooth Star block and now have three units ready to sew together. Here they are from the front . . .
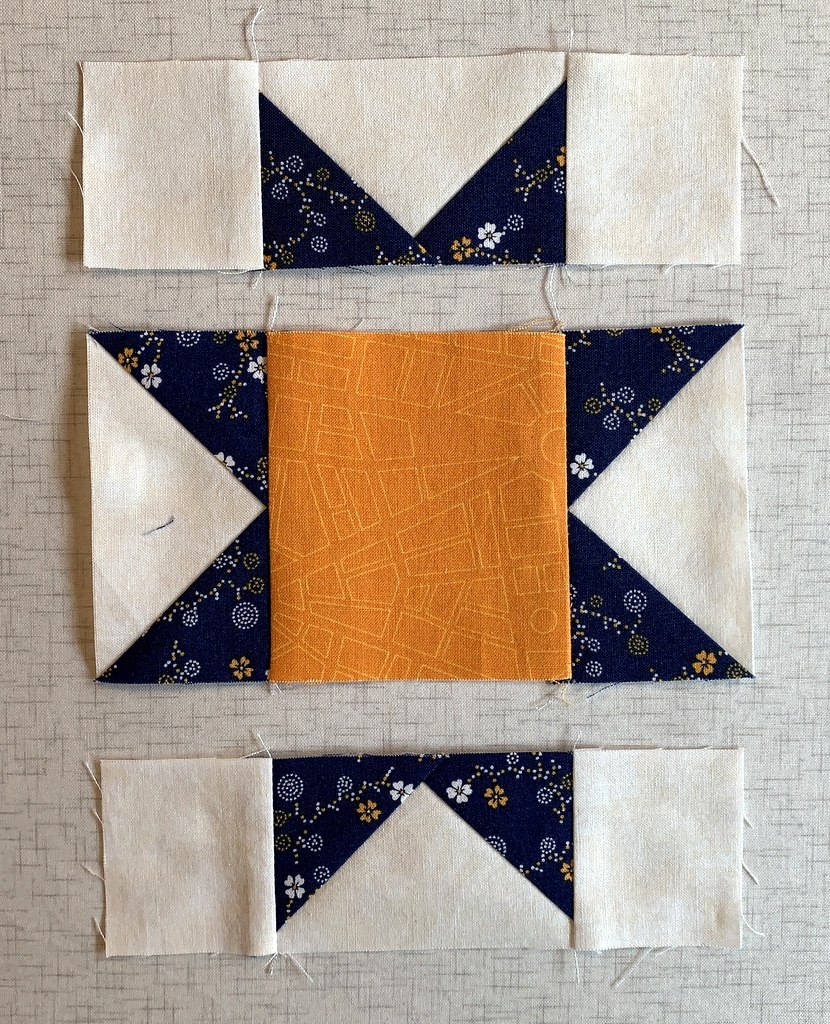
. . . and from the back:

Even though the seams are pressed in opposite directions where they will meet, I still pin the intersections and add the all-important No Surprises pin at the end:

Do you see how the edges at the beginning of the stitching line (upper left corner) don’t meet? They’re supposed to. To correct this I’ve added a pin at the beginning of the stitching line to nudge that top layer over to meet its neighbor underneath:

These two seams that I’m sewing are the ones that connect my Flying Geese units to the middle section. When I get to the middle of the block I’ll make sure my stitching line is a couple of threads away from the point and toward the raw edges (Tip #3).
The seams are sewn and pressed toward the outside:

This is the way I pressed my star block seams for years. The block still looks good from the front but it feels bulky at the V where all those layers are lying on top of each other. Nowadays I clip the seam at the intersections so that I can press it toward center of the block, minimizing the bulk at the V:

Another option is to make a second clip on the other side of the intersection and press the seam open just between the clips, revealing a tiny 4-patch design. That’s what I showed you in my last post:
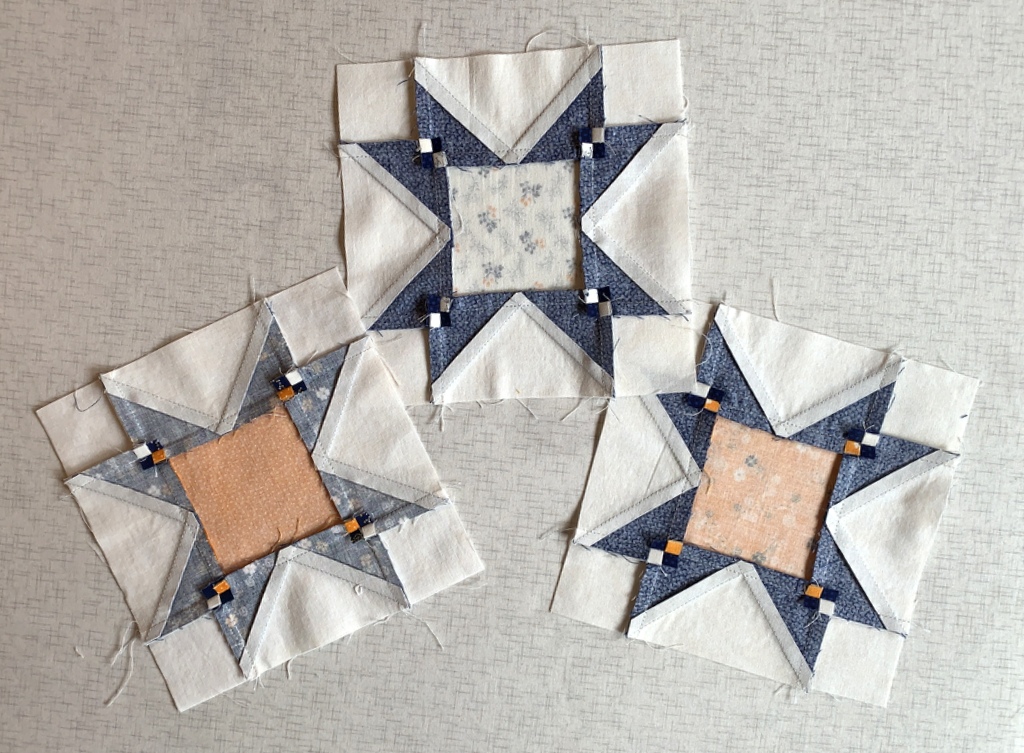
Here are my three most recent 6″ Sawtooth Star blocks, including the one starring (sorry, couldn’t resist) in this post:

I hope you found my tips helpful. Please let me know if you have any questions!
Update: to take a look at Scattered Stars, the quilt these star blocks were made for, click here.